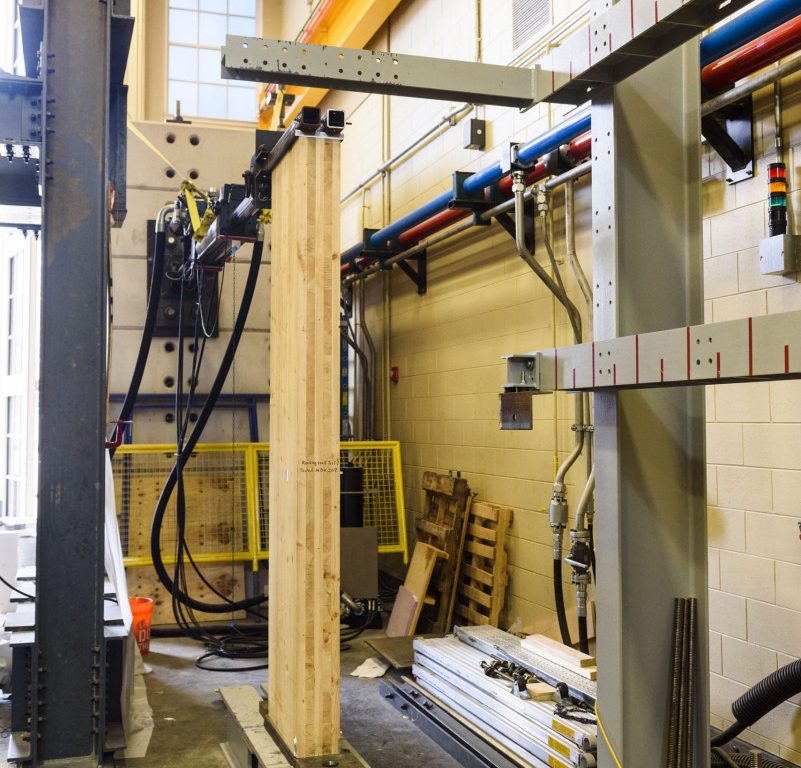
Large Scale Structures Laboratory
The Center for Sustainable Infrastructure is closely aligned with UA’s Large Scale Structures Laboratory (LSSL). Housed in the South Engineering Research Center, the LSSL contains a 75-foot by 40-foot test floor with a 3-foot thick strong floor, two 15-ton capacity overhead cranes, and 7-foot-by-4-inch by 7-foot-by-4-inch and 2-foot thick reconfigurable reinforced-concrete blocks that can be stacked and post-tensioned to the strong floor to provide reaction walls on the testing floor. The centerpiece of the LSSL is a 13-foot by 12-foot uniaxial earthquake simulator capable of exciting a 40,000-pound payload to a peak acceleration of 1.2 g, displacement of plus/minus 20 inches, and maximum velocity of 45 inches per second within a frequency range of 0 to 30 Hertz. In addition, the LSSL contains a 10-foot by 10-foot by 10-foot soil pit adjacent to the strong floor, with 5-ton capacity overhead crane, for geotechnical-related investigations including reduced-scale study of soil-structure interaction.
In addition to the earthquake simulator, the laboratory is equipped with a suite of eight MTS hydraulic actuators with large-flow servo valves, ranging in capacity from 35 to 330 kips, a high-capacity distribution system powered by an MTS Silent Flow Pump that can provide up to 720 GPM flow of high-pressure hydraulic fluid, service manifolds and several digital controllers. The LSSL is also well equipped with instrumentation including an OptiTrack optical motion capture device, accelerometers, LVDT’s, load cells, etc., and National Instruments high-speed data acquisition systems.